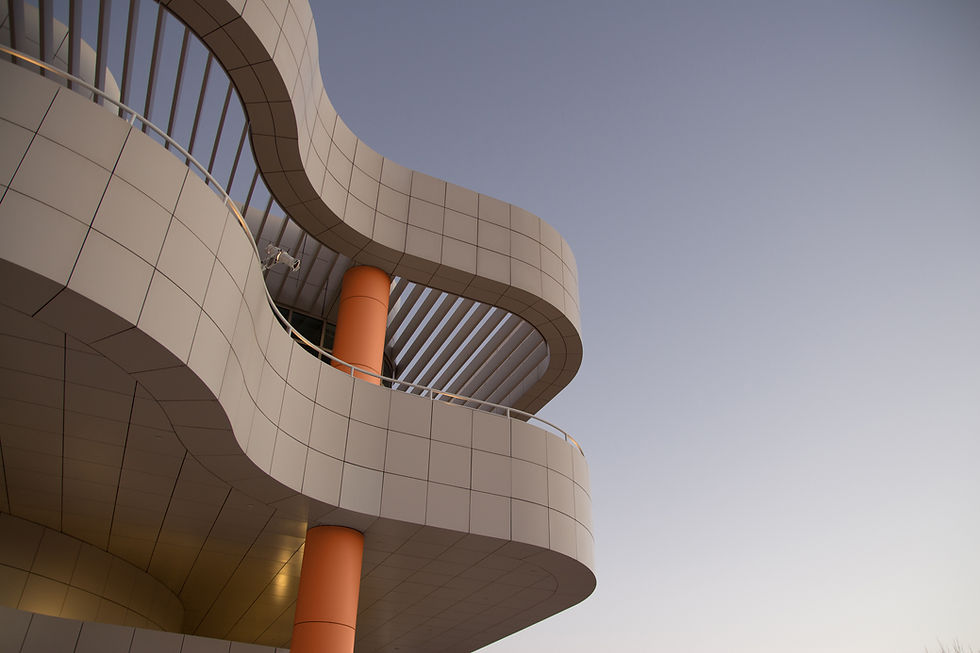
The Top Resources for Training Your Team: A Guide for Plant Managers
As a plant manager, one of the most essential aspects of your role is ensuring that your team operates at peak efficiency, safety, and effectiveness. A well-trained workforce not only enhances productivity but also fosters a culture of continuous improvement. With that in mind, investing in training programs and resources that empower your team is critical. In this blog, we'll explore the top resources you should consider for training your team, ensuring they have the skills, knowledge, and confidence to thrive in their roles.
1. In-House Training Programs
In-house training programs are tailored to your specific plant's operations, products, and challenges. By designing your own training modules, you can address the exact skills your team needs without spending time on generic content. Whether it’s training new hires on plant safety protocols or advanced training for seasoned employees on new technologies, customized in-house training can have a huge impact.
Benefits:
Direct relevance to your plant’s operations.
Flexibility in scheduling and content.
Opportunity for hands-on learning and mentorship from experienced staff.
Tip: Consider collaborating with department heads and supervisors to identify the most common gaps in skills and knowledge across your workforce, ensuring your training focuses on what matters most.

2. Online Learning Platforms
In today’s digital age, online learning platforms are an indispensable resource for training your team. Websites like LinkedIn Learning, Coursera, and Udemy offer a wide range of courses on leadership, plant management, safety, and technical skills. These platforms are particularly useful for employees who need flexible training options or want to pursue self-paced learning.
Benefits:
Access to a broad array of training topics.
Flexible and scalable for teams of all sizes.
Convenient learning that employees can complete during off-peak hours.
Tip: While online learning is effective for many topics, it’s best used in conjunction with hands-on training for practical skills that require more direct supervision.
3. Industry Certifications and Accreditations
Industry certifications are often essential for ensuring that your team is knowledgeable and up-to-date on best practices, safety standards, and regulations. Look for certification programs that are specific to manufacturing, plant operations, and safety. Organizations such as OSHA (Occupational Safety and Health Administration) and the American Society of Mechanical Engineers (ASME) offer various certifications that can elevate your team’s expertise.
Benefits:
Demonstrates a commitment to industry standards.
Improves team confidence in their abilities.
Can boost your plant’s reputation for adhering to best practices.
Tip: Encourage employees to pursue certifications that align with their career aspirations, while also meeting the plant's needs.
4. Plant Manager Mentorship Programs
A mentorship program can significantly enhance the development of both new and existing team members. Pairing less experienced employees with seasoned veterans allows for knowledge transfer, practical guidance, and the development of leadership skills. Mentors can provide insights that formal training might not cover, especially when it comes to real-world problem-solving.
Benefits:
Personalized, one-on-one guidance.
Builds a strong sense of teamwork and culture.
Helps develop leadership and communication skills within your team.
Tip: Create a formal mentorship structure with clear goals and expectations for both mentors and mentees to maximize the program’s effectiveness.
5. Simulations and Virtual Training
Plant managers can leverage technology to create realistic simulations for training purposes. Simulations are especially useful for safety training, troubleshooting scenarios, and equipment handling. Virtual reality (VR) and augmented reality (AR) are increasingly used in industrial environments to replicate plant operations in a safe, controlled environment.
Benefits:
Realistic, hands-on experience without the risks of a live environment.
Enhances learning retention by engaging employees in interactive scenarios.
Scalable for various team sizes and plant layouts.
Tip: Invest in simulation technology that replicates the equipment and processes specific to your plant for maximum relevance and effectiveness.
6. Workshops and Industry Conferences
Attending workshops and industry conferences allows your team to stay on top of the latest trends, technologies, and regulations in plant management. These events provide valuable networking opportunities and can give your employees fresh perspectives on plant operations and strategies. Additionally, many workshops offer specialized training that can be directly applied to your facility.
Benefits:
Exposure to the latest trends and technologies in the industry.
Networking opportunities with other plant managers and professionals.
Access to expert-led sessions and practical workshops.
Tip: Send different team members to workshops that align with their specific roles, so they can return with new knowledge and ideas that benefit the entire plant.
7. Vendor and Supplier Training
Many vendors and suppliers offer training on how to effectively use and maintain the equipment and materials they provide. Taking advantage of these training opportunities ensures that your team can fully utilize the tools and machinery at their disposal. This training also promotes a deeper understanding of your supply chain and equipment specifications.
Benefits:
Tailored training on your plant’s specific equipment.
Direct insights into the best practices for using and maintaining machinery.
Strengthens relationships with suppliers and vendors.
Tip: Schedule regular refresher courses for equipment and tool training, especially when you integrate new technology into your plant’s operations.
8. Safety Training Resources
Safety is paramount in any industrial setting, and having a robust safety training program is essential. Many organizations, such as the National Safety Council (NSC), provide specialized safety training for plant workers. Topics such as machine safety, emergency response, and workplace hazard identification are key areas to cover.
Benefits:
Reduced risk of accidents and injuries.
Increased employee awareness of safety protocols.
Compliance with legal safety requirements.
Tip: Make safety training an ongoing effort with regular updates and drills to keep safety at the forefront of your team’s operations.
Conclusion
Training your team is an ongoing investment that pays dividends in increased productivity, safety, and overall team morale. By leveraging a combination of in-house training programs, online platforms, industry certifications, mentorship, and advanced technologies, you can ensure your team has the skills necessary to excel in their roles.
Additionally, continuously refining your training strategies will help your plant maintain a competitive edge and meet the evolving challenges of the industry.
At Top Quality Recruitment (TQR), we understand the importance of having a well-trained workforce, and we’re here to help you find the best candidates to fit your plant's needs. For expert staffing solutions and advice, feel free to get in touch with us today!